
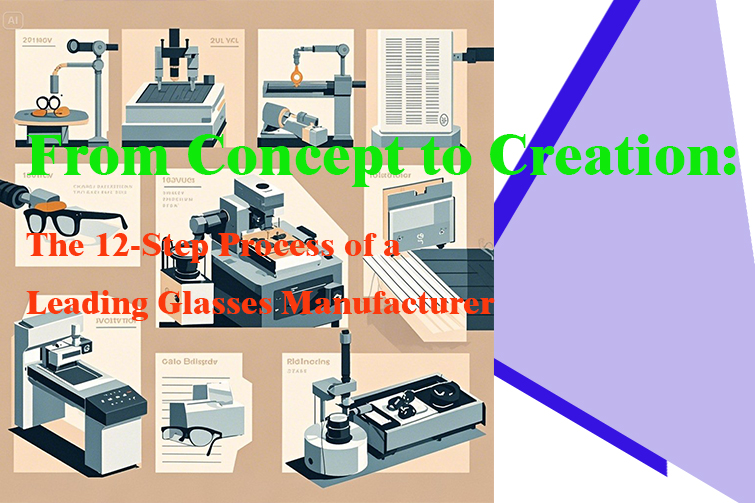
From Concept to Creation: The 12-Step Process of a Leading Glasses Manufacturer
- Introduction In the bustling eyewear market, the decision of which glasses manufacturer to partner with can be the pivot point between a brand's success and failure. Whether you're a fledgling startup aiming to disrupt the market with trendy eyewear or an established enterprise seeking to expand your product range, making an informed choice is non - negotiable. Given that a staggering 80% of partnerships crumble due to unmet expectations (Deloitte), a comprehensive evaluation of OEM/ODM criteria is not just advisable—it's essential. This article serves as your compass, guiding you through the intricate process of choosing a glasses manufacturer that aligns perfectly with your brand's goals. The Pillars of Selection: Key Criteria to Consider Technical Proficiency and Innovation 1. Material Expertise
- A top - tier glasses manufacturer should possess an in - depth understanding of a diverse range of materials. For instance, expertise in handling titanium is highly sought - after. Titanium frames are renowned for their lightweight yet robust nature, and a manufacturer well - versed in working with this material can craft high - end products. Similarly, proficiency in using bio - based acetates, which are sustainable alternatives, or medical - grade plastics for prescription eyewear, showcases their adaptability. Consider a manufacturer that specializes in creating frames from recycled ocean plastics. Their unique knowledge of this material allows them to produce eco - friendly eyewear that caters to environmentally conscious consumers. 2. Advanced Technological Adoption
- The use of advanced manufacturing technologies is a telltale sign of a forward - thinking manufacturer. 3D printing, for example, has revolutionized eyewear production. It enables the creation of intricate and customized frame designs that were previously challenging or impossible to achieve. AI - driven quality control ensures that each pair of glasses meets the highest standards, minimizing defects significantly. AR prototyping is another game - changing technology. Brands can use this to visualize and approve designs in real - time, slashing the time and cost associated with traditional prototyping methods. Companies like Oakley have successfully collaborated with manufacturers leveraging 3D - printed hinges to develop lightweight and innovative sports frames, highlighting the power of such technologies. 3. Patented Innovations
- Patents are a clear indication of a manufacturer's dedication to innovation. EssilorLuxottica, with over 2,000 patents, is a prime example. These patents cover everything from lens technologies to frame designs. A manufacturer with a strong patent portfolio can offer unique product features that set your brand apart in the market. Quality Assurance: The Cornerstone of Success 1. Certification Adherence
- For manufacturers involved in producing prescription eyewear, ISO certifications such as ISO 9001/13485 for medical devices are imperative. These certifications guarantee that the manufacturing processes adhere to strict quality management and medical device standards. Brands should not compromise on this aspect, as it reflects the manufacturer's ability to produce safe and high - quality eyewear. 2. Rigorous Testing Regimes
- A reliable manufacturer will subject their products to a battery of tests. Salt spray tests, which simulate harsh environmental conditions, should demonstrate a minimum of 5 - year corrosion resistance. Stress bending tests, where frames are bent over 10,000+ cycles, ensure durability. Additionally, UV protection validation is crucial, especially for sunglasses, to safeguard the wearer's eyes. By examining these testing results, brands can be confident in the long - term performance of the eyewear. For example, if a manufacturer claims their sunglasses provide 100% UV protection, they should be able to back it up with proper testing documentation. 3. Customer Feedback Analysis
- Looking at customer feedback from well - known brands like Warby Parker can offer valuable insights. Positive reviews regarding a manufacturer's quality are a good sign, while negative feedback should raise red flags. This feedback can cover aspects such as the durability of the frames, the clarity of the lenses, and the overall customer experience. Customization and Design Support 1. Design Collaboration
- For OEM/ODM partnerships, design collaboration is of utmost importance. A manufacturer that offers in - house designers or CAD (Computer - Aided Design) support can help bring your brand's vision to fruition. In - house designers can provide creative input, while CAD support allows for precise design adjustments and mock - ups. Imagine a brand that wishes to create a unique line of cat - eye sunglasses. A manufacturer with experienced designers can offer suggestions on frame shapes, colors, and materials, while CAD technology can be used to create detailed 3D models for approval. 2. Material Flexibility
- The ability to source sustainable materials or rare metals is a significant advantage. Sustainable materials, such as recycled titanium or plant - based plastics, are in high demand as consumers become more environmentally conscious. On the other hand, rare metals can add a touch of luxury to high - end eyewear. A manufacturer that can offer a wide range of material options gives brands the flexibility to target different market segments. For example, a brand aiming for a premium, eco - friendly market can work with a manufacturer that specializes in sustainable materials. 3. Minimum Order Quantity (MOQ) Considerations
- MOQs vary depending on the manufacturer and the type of product. Startups may benefit from manufacturers with small MOQs, such as 50 - 100 units. This allows them to test the market without a large upfront investment. Larger brands, however, may require manufacturers with scalable capacity to handle orders of 100,000+ units without sacrificing quality. McKinsey's data showing that brands offering customization see 40% higher customer retention emphasizes the importance of working with a manufacturer that can accommodate customization requests, regardless of the order size. Production Capacity and Lead Times 1. Scalability
- A manufacturer should be able to scale production according to market demand. Whether it's ramping up production for a new product launch or handling increased orders during peak seasons, they should be able to do so without a drop in quality. A manufacturer with state - of - the - art production facilities and a skilled workforce is more likely to achieve this. For example, if a brand experiences a sudden surge in demand for a particular style of glasses, the manufacturer should be able to quickly adjust production lines to meet this demand. 2. Lead Time Management
- Lead times can make or break a brand's ability to meet market expectations. The average production time for eyewear ranges from 4 - 12 weeks. However, delays can be costly. According to APQC, a mid - sized brand can lose up to $250,000 per month due to production delays. Brands should inquire about the manufacturer's lead time and their track record in meeting deadlines. Additionally, a manufacturer should have contingency plans in place. This includes having backup suppliers for raw materials and disaster recovery protocols to ensure that production can continue even in the face of unforeseen events. Ethical and Sustainable Practices 1. Supply Chain Traceability
- In an era of increasing consumer awareness, supply chain traceability is crucial. A manufacturer that uses blockchain technology for material sourcing allows brands to track the origin of materials from the mine to the final product. This transparency builds trust with consumers, especially when it comes to issues like conflict - free sourcing. 2. Eco - Friendly Initiatives
- Manufacturers that embrace eco - friendly initiatives, such as using recycled materials, solar energy in production, or carbon - neutral shipping, are more likely to appeal to environmentally conscious consumers. Nielsen reports that 73% of buyers prefer sustainable brands, making this an important consideration for brands looking to partner with a manufacturer. For example, a manufacturer that uses recycled aluminum for frame production and ships products in biodegradable packaging is not only reducing its environmental impact but also aligning with the values of a growing consumer segment. 3. Fair Labor Practices
- Ensuring compliance with labor standards, such as SA8000, is essential. This standard covers areas like fair wages, safe working conditions, and no child labor. Brands should verify that the manufacturer adheres to these standards to avoid any ethical controversies. Intellectual Property Protection 1. Non - Disclosure Agreements (NDAs)
- NDAs are a fundamental tool for protecting your brand's designs. When sharing design concepts with a manufacturer, an NDA ensures that the manufacturer cannot disclose or use these designs for other clients. This protects your brand's intellectual property and gives you a competitive edge in the market. 2. Patent Filing Support
- Some manufacturers, like JINS, assist clients in securing design patents. This support can be invaluable for brands, especially those new to the process. A manufacturer that understands the patent - filing process can help you protect your unique designs from being copied by competitors. 3. Copyright Ownership
- It's important to clarify who retains the rights to prototypes. Whether it's the brand or the manufacturer, clear ownership rights prevent any disputes down the line. This ensures that your brand has full control over its intellectual property assets. Post - Production Support 1. Repair Services and Warranty Programs
- A manufacturer that offers repair services and warranty programs can significantly reduce customer churn. Brands can pass on these benefits to consumers, increasing customer satisfaction and loyalty. For example, a manufacturer that provides a 2 - year warranty on frames and offers easy - to - access repair services gives consumers peace of mind. 2. Logistics Solutions
- Eco - friendly packaging and global shipping capabilities are important post - production services. Eco - friendly packaging aligns with sustainable practices, while global shipping ensures that your products can reach customers worldwide. A manufacturer that can handle these logistics efficiently can streamline your supply chain. 3. Data Analytics and Insights
- Shared sales insights can help brands optimize future collections. A manufacturer that analyzes sales data can provide valuable information on which products are selling well, which styles are trending, and which markets are most profitable. This data - driven approach can help brands make informed decisions about product development and marketing strategies. The Impact of a Right Manufacturer Selection 1. Cost Savings
- Partnering with the right manufacturer can lead to substantial cost savings. IndustryWeek reports that a mismatched partner can increase costs by 20 - 30%. The right manufacturer can offer competitive pricing, efficient production processes, and help avoid costly mistakes such as defective products or production delays. 2. Market Differentiation
- Exclusive designs and superior quality, which are more likely to be achieved with a reliable manufacturer, can drive premium pricing. A unique product offering can set your brand apart in a crowded market, attracting customers who are willing to pay more for high - quality, distinctive eyewear. 3. Risk Mitigation
- Robust quality control, as provided by a top - tier manufacturer, reduces the risk of product recalls. Recalls can be extremely costly in terms of both financial losses and damage to a brand's reputation. By choosing a manufacturer with strict quality assurance protocols, brands can mitigate these risks. Conclusion Selecting a glasses manufacturer is a multifaceted process that demands careful consideration of various OEM/ODM criteria. By evaluating a manufacturer's technical expertise, quality assurance, customization capabilities, production capacity, ethical practices, intellectual property protection, and post - production support, brands can make an informed decision. The right manufacturer can be a strategic partner, helping brands achieve cost savings, market differentiation, and risk mitigation. Use this eyewear manufacturer evaluation checklist as a guide to choose an eyewear supplier or private label glasses manufacturer that will propel your brand to success in the eyewear market.
Conclusion
The glasses manufacturing process is a testament to precision and innovation. By following this 12-step workflow, manufacturers deliver products that balance quality, sustainability, and style. Partnering with a manufacturer that prioritizes efficiency and transparency ensures your brand stays ahead in a competitive market.
Ready to explore our end-to-end production capabilities? Contact us to discuss how we can bring your eyewear vision to life.